陶瓷板的破坏主要是因裂痕不安定传播所造成,刀具在加工时的刀尖作用、在已加工表面上会留下某种程度的尖锐加工痕迹,产生细小的裂痕缺陷和应力集中现象,降低结构陶瓷零件的疲劳强度,影响功能陶瓷板的电、磁特性。所以对陶瓷板必须进行超精密加工,减小细小的裂痕缺陷和应力集中,提高零件的疲劳强度。
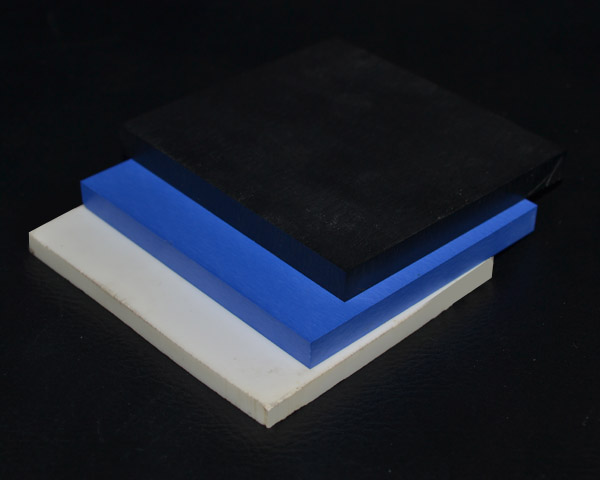
通常,将达到或超过本时代精度界限的高精度加工为陶瓷超精密加工,在20世纪80年代,加工精度在0.05um精度的加工技术称为超精密加工;到2000年,超精密加工精度可达Inm以下。超精密加工技术是一门新兴的综合新型加工技术。它集成了现代机械、光学、计算机、测量及材料等先进技术成就,使得超精密加工的精度从20世纪60年代的微米级提高到目前的纳米级,极大地提高了产品的性能和可靠性。超精密加工方法主要有超精密切削、超精密磨削、超精密研磨。
超精密切削主要是用高精度的机床和单晶金刚石刀具进行的切削加工方法。超精密切削可用于加工感光鼓、磁盘、磁鼓、大功率的反射镜.以及平面、球面或多面棱镜等中小型超精密零件。
超精密磨削是利用分布在砂轮表面上磨粒的切削刃对工件的切削作用进行的。由于磨削加工T具砂轮是用磨料的许多微小切削刃进行切削,所排除的切削量也极微小,所以加工精度高。但由于磨削是面状刀具与工件的作用,因此,与单刃刀具相比,其产生的磨削阻力要大数倍乃至百倍。为了获得高的磨削精度,必须要有高刚度的砂轮和磨床。
陶瓷抛光是通过介于工件和研具间的游离磨粒及加工液与工件及研具相互机械摩擦,或在机械、化学及其它物理现象的作用下实现材料的微量切削,使工件达到所要求达到的几何尺寸和表面粗糙度(≤0. Ium)精度的加工方法。抛光工艺必须是在研磨加工完成的基础上进行,要求使用微细的磨料,组织均匀细致的抛光盘,能分散磨料的抛光液,抛光盘和加工夹具要求在蒸馏水和超纯水中洗净尘埃,还要有无尘化的环境。主要适应于对功能陶瓷材料元件的高表面精度和极小加工变质层、保证元件功能的加工要求。
晶体材料的无损伤表面抛光技术是以不破坏极表层结晶结构而进行的材料微量切除加工方法。可以按照加工状态,将无损伤抛光看作是机械作用和化学作用所进行的。为了保证各种功能陶瓷材料制成的电子和光学无件的性能,目前已开发了一系列的无加工变质层、无表面损伤(不扰乱结晶的原子排列)的镜面超精密抛光方法。此外,现在还出现了半导体材料的化学抛光、电化学抛光、超声波振动抛光以及油石抛光等新技术。
通常,将达到或超过本时代精度界限的高精度加工为陶瓷超精密加工,在20世纪80年代,加工精度在0.05um精度的加工技术称为超精密加工;到2000年,超精密加工精度可达Inm以下。超精密加工技术是一门新兴的综合新型加工技术。它集成了现代机械、光学、计算机、测量及材料等先进技术成就,使得超精密加工的精度从20世纪60年代的微米级提高到目前的纳米级,极大地提高了产品的性能和可靠性。超精密加工方法主要有超精密切削、超精密磨削、超精密研磨。
超精密切削主要是用高精度的机床和单晶金刚石刀具进行的切削加工方法。超精密切削可用于加工感光鼓、磁盘、磁鼓、大功率的反射镜.以及平面、球面或多面棱镜等中小型超精密零件。
超精密磨削是利用分布在砂轮表面上磨粒的切削刃对工件的切削作用进行的。由于磨削加工T具砂轮是用磨料的许多微小切削刃进行切削,所排除的切削量也极微小,所以加工精度高。但由于磨削是面状刀具与工件的作用,因此,与单刃刀具相比,其产生的磨削阻力要大数倍乃至百倍。为了获得高的磨削精度,必须要有高刚度的砂轮和磨床。
陶瓷抛光是通过介于工件和研具间的游离磨粒及加工液与工件及研具相互机械摩擦,或在机械、化学及其它物理现象的作用下实现材料的微量切削,使工件达到所要求达到的几何尺寸和表面粗糙度(≤0. Ium)精度的加工方法。抛光工艺必须是在研磨加工完成的基础上进行,要求使用微细的磨料,组织均匀细致的抛光盘,能分散磨料的抛光液,抛光盘和加工夹具要求在蒸馏水和超纯水中洗净尘埃,还要有无尘化的环境。主要适应于对功能陶瓷材料元件的高表面精度和极小加工变质层、保证元件功能的加工要求。
晶体材料的无损伤表面抛光技术是以不破坏极表层结晶结构而进行的材料微量切除加工方法。可以按照加工状态,将无损伤抛光看作是机械作用和化学作用所进行的。为了保证各种功能陶瓷材料制成的电子和光学无件的性能,目前已开发了一系列的无加工变质层、无表面损伤(不扰乱结晶的原子排列)的镜面超精密抛光方法。此外,现在还出现了半导体材料的化学抛光、电化学抛光、超声波振动抛光以及油石抛光等新技术。
地址:http://www.taocibang.cn/jishu/525.html
本文“陶瓷板精密加工技术”由科众陶瓷编辑整理,修订时间:2019-03-16 16:43:19
科众陶瓷是专业的工业陶瓷加工生产厂家,可来图来样按需定制,陶瓷加工保证质量、交期准时!