氧化铝陶瓷
氧化铝陶瓷是用途最广泛,原料最丰富,价格最低廉的一种高温结构陶瓷,是研究得最成熟的高熔点氧化物陶瓷,在机械,化工,电子等领域具有广泛的用途。氧化铝原料来源丰富,价格低廉。按组成可将其分为氧化铝瓷和高铝瓷两大类。
氧化铝陶瓷中一般氧化铝含量在99%以上,烧结温度高当原料粒度较粗时,烧结温度可达1700℃:为了改善烧结性能,降低烧结温度,往往添加少量MgO、Cr2 03、Ti02等作为烧结助剂,利用生成固溶体或者生成晶界相,活化晶格,抑制晶粒长大,从而促进烧结,陶瓷材料的烧结属固相烧结机理。烧结后材料的主晶相为刚玉相,性能较好。氧化铝陶瓷具有如下特性:①力学性能高;②电阻率高;③硬度高;④熔点高、耐腐蚀;⑤优良的光学特性;⑥离子导电性。
高铝瓷泛指95瓷、90瓷、85瓷、75瓷等不同氧化铝含量的陶瓷,添加了不同数量的硅酸盐液相烧结助剂或者其他物质,因而烧结温度较低,同时材料性能相对于氧化铝瓷也有所下降,根据生成的主晶相含量,分为刚玉瓷、刚玉一莫来石瓷、莫来石瓷。
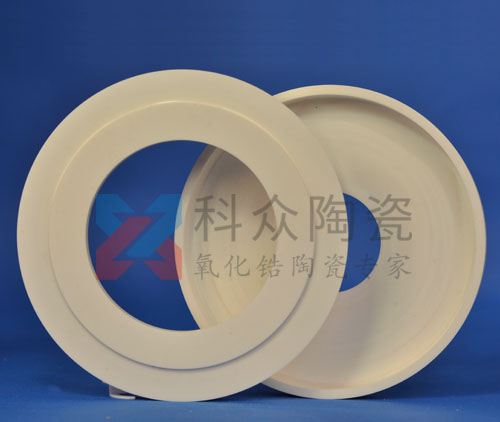
氧化铝
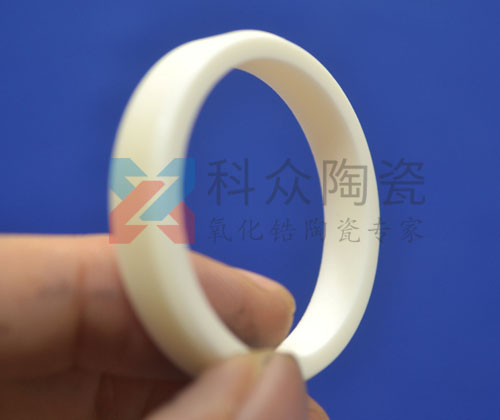
氧化锆
氧化铝陶瓷是用途最广泛,原料最丰富,价格最低廉的一种高温结构陶瓷,是研究得最成熟的高熔点氧化物陶瓷,在机械,化工,电子等领域具有广泛的用途。氧化铝原料来源丰富,价格低廉。按组成可将其分为氧化铝瓷和高铝瓷两大类。
氧化铝陶瓷中一般氧化铝含量在99%以上,烧结温度高当原料粒度较粗时,烧结温度可达1700℃:为了改善烧结性能,降低烧结温度,往往添加少量MgO、Cr2 03、Ti02等作为烧结助剂,利用生成固溶体或者生成晶界相,活化晶格,抑制晶粒长大,从而促进烧结,陶瓷材料的烧结属固相烧结机理。烧结后材料的主晶相为刚玉相,性能较好。氧化铝陶瓷具有如下特性:①力学性能高;②电阻率高;③硬度高;④熔点高、耐腐蚀;⑤优良的光学特性;⑥离子导电性。
高铝瓷泛指95瓷、90瓷、85瓷、75瓷等不同氧化铝含量的陶瓷,添加了不同数量的硅酸盐液相烧结助剂或者其他物质,因而烧结温度较低,同时材料性能相对于氧化铝瓷也有所下降,根据生成的主晶相含量,分为刚玉瓷、刚玉一莫来石瓷、莫来石瓷。
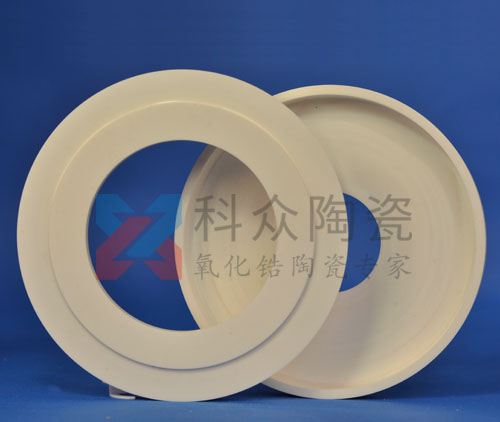
氧化铝
氧化锆陶瓷
1)氧化锆陶瓷的晶体结构及马氏体相变
氧化锆有立方( Cubic)、四方(Tetragonal)和单斜(Monoclinic)三种晶型,单斜相是低温稳定相,如果将它加热到1000℃以上转变为四方相,继续升温至2370℃,则转变为立方相。
2)氧化锆相变增韧机理
氧化锆相变增韧机理主要分为应力诱导相变增韧和微裂纹增韧。
(1)应力诱导相变增韧。四方相氧化锆颗粒在应力作用下,发生向单斜相的转变,随着相变的进行,伴有体积膨胀和切应变,并吸收能量,使裂纹扩展阻力增加,起到增韧的
作用。
(2)微裂纹增韧。在使用温度下,如果ZrO2晶粒大于临界粒径,四方相晶粒自发相变为单斜相,由于体积膨胀在其周围产生许多微裂纹或裂纹核,当它们处于主裂纹前的作用区内时,由于它们延伸释放主裂纹的部分应变能,增加了主裂纹扩展所需的能量,从而有效地制了裂纹扩展,提高了材料的断裂韧性,材料的弹性应变能多转换为微裂纹的新生表面能。
3)氧化锆陶瓷的类型及其特点
根据相结构的稳定性,氧化锆陶瓷分为稳定ZrO2陶瓷和部分稳定ZrO2陶瓷。
1)氧化锆陶瓷的晶体结构及马氏体相变
氧化锆有立方( Cubic)、四方(Tetragonal)和单斜(Monoclinic)三种晶型,单斜相是低温稳定相,如果将它加热到1000℃以上转变为四方相,继续升温至2370℃,则转变为立方相。
2)氧化锆相变增韧机理
氧化锆相变增韧机理主要分为应力诱导相变增韧和微裂纹增韧。
(1)应力诱导相变增韧。四方相氧化锆颗粒在应力作用下,发生向单斜相的转变,随着相变的进行,伴有体积膨胀和切应变,并吸收能量,使裂纹扩展阻力增加,起到增韧的
作用。
(2)微裂纹增韧。在使用温度下,如果ZrO2晶粒大于临界粒径,四方相晶粒自发相变为单斜相,由于体积膨胀在其周围产生许多微裂纹或裂纹核,当它们处于主裂纹前的作用区内时,由于它们延伸释放主裂纹的部分应变能,增加了主裂纹扩展所需的能量,从而有效地制了裂纹扩展,提高了材料的断裂韧性,材料的弹性应变能多转换为微裂纹的新生表面能。
3)氧化锆陶瓷的类型及其特点
根据相结构的稳定性,氧化锆陶瓷分为稳定ZrO2陶瓷和部分稳定ZrO2陶瓷。
氧化锆
科众工业陶瓷厂是结构陶瓷专家,结构陶瓷,厂家直销,价格有优势;结构陶瓷成型/烧结/精密加工工艺成熟、交期准、保障质量,欢迎来电咨询:13412443344/0769-33235150/QQ921105260
地址:http://www.taocibang.cn/jishu/1311.html
本文“工程陶瓷材料”由科众陶瓷编辑整理,修订时间:2017-07-11 16:13:49
科众陶瓷是专业的工业陶瓷加工生产厂家,可来图来样按需定制,陶瓷加工保证质量、交期准时!
- 上一页:陶瓷轮膜成型法
- 下一页:挤压成型工艺原理及特点