工程陶瓷大背吃刀量缓进给磨削
科众陶瓷厂是一家生产加工陶瓷零件的生产厂家,大背吃刀量缓进给磨削是指在磨削过程中砂轮吃刀量比常规磨削大、工件进给速度低的磨削方法。相比常规磨削,工程陶瓷的这种磨削加工方法可以获得较高的加工效率和较低的表面粗糙度,是加工工程陶瓷的主要磨削方法,可分为杯形砂轮端面磨削和陶瓷球磨罐平形砂轮磨削两种。
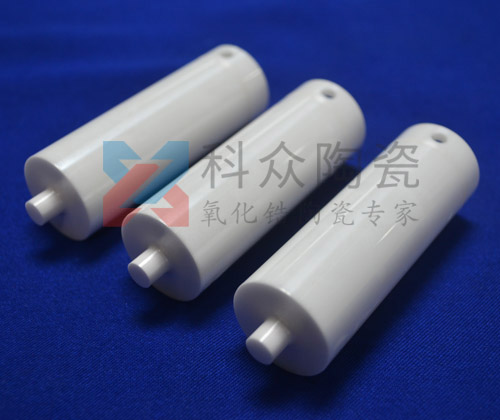
氧化锆陶瓷
工程陶瓷杯形砂轮大背吃刀量缓进给端面磨削
用杯形砂轮进行端面磨削时,砂轮轴与工件平面的法向平行安装。在磨削工件过程中,切削刃可以分为三个磨削部分:主磨削部分、过渡区部分、修磨部分,主磨削部分承受的磨削力最大,材料发生大规模挤裂,形成较大的颗粒状或薄片状磨屑,并在切削表面上留下凹痕,是纺织陶瓷材料的主要去除区;过渡区部分承受的磨削力逐渐减小,材料去除由大规模挤裂向小规模挤裂过渡,刀具前方的材料发生微细的破碎;修磨部分承受的磨削力较小,材料的去除量很小,生成磨削表面较平滑的部分,起到修形的作用。
杯形砂轮端面磨削是适于硬脆材料的高效率、低成本磨削加工技术。该方法的优点是残留在磨削表面上的裂纹较少,可以获得完整的被加工表面,砂轮的磨损量很小,不需要经常修整;缺点是砂轮磨削力和磨削功率比较大,会产生大量磨削热。目前对于端面磨削的研究大部分都集中在磨削热和提高材料去除率方面,而在实现端面磨削的数控加工中,所需的刀具轨迹规划并没有太多的研究。
点胶陶瓷在加工过程中应用的轨迹规划方法,主要包括等参数线法、等截距偏置法、等残留高度法、空间填充法等。这些方法各有优点,有的算法简单,计算量小,有的效率高,有的加工精度高。然而这些方法都是针对铣削加工而言的,要实现端面陶瓷法兰磨削的实际数控加工,对轨迹规划的研究十分必要。
科众工业陶瓷厂是【结构陶瓷】专家,【结构陶瓷】厂家直销,价格有优势;【结构陶瓷】成型/烧结/精密加工工艺成熟、交期准、保障质量,欢迎来电咨询:13412443344/0769-33235150/QQ2712136085科众工业陶瓷厂是【结构陶瓷】专家,【结构陶瓷】厂家直销,价格有优势;【结构陶瓷】成型/烧结/精密加工工艺成熟、交期准、保障质量,欢迎来电咨询:13412443344/0769-33235150/QQ2712136085
科众陶瓷厂是一家生产加工陶瓷零件的生产厂家,大背吃刀量缓进给磨削是指在磨削过程中砂轮吃刀量比常规磨削大、工件进给速度低的磨削方法。相比常规磨削,工程陶瓷的这种磨削加工方法可以获得较高的加工效率和较低的表面粗糙度,是加工工程陶瓷的主要磨削方法,可分为杯形砂轮端面磨削和陶瓷球磨罐平形砂轮磨削两种。
氧化锆陶瓷
工程陶瓷杯形砂轮大背吃刀量缓进给端面磨削
用杯形砂轮进行端面磨削时,砂轮轴与工件平面的法向平行安装。在磨削工件过程中,切削刃可以分为三个磨削部分:主磨削部分、过渡区部分、修磨部分,主磨削部分承受的磨削力最大,材料发生大规模挤裂,形成较大的颗粒状或薄片状磨屑,并在切削表面上留下凹痕,是纺织陶瓷材料的主要去除区;过渡区部分承受的磨削力逐渐减小,材料去除由大规模挤裂向小规模挤裂过渡,刀具前方的材料发生微细的破碎;修磨部分承受的磨削力较小,材料的去除量很小,生成磨削表面较平滑的部分,起到修形的作用。
杯形砂轮端面磨削是适于硬脆材料的高效率、低成本磨削加工技术。该方法的优点是残留在磨削表面上的裂纹较少,可以获得完整的被加工表面,砂轮的磨损量很小,不需要经常修整;缺点是砂轮磨削力和磨削功率比较大,会产生大量磨削热。目前对于端面磨削的研究大部分都集中在磨削热和提高材料去除率方面,而在实现端面磨削的数控加工中,所需的刀具轨迹规划并没有太多的研究。
点胶陶瓷在加工过程中应用的轨迹规划方法,主要包括等参数线法、等截距偏置法、等残留高度法、空间填充法等。这些方法各有优点,有的算法简单,计算量小,有的效率高,有的加工精度高。然而这些方法都是针对铣削加工而言的,要实现端面陶瓷法兰磨削的实际数控加工,对轨迹规划的研究十分必要。
科众工业陶瓷厂是【结构陶瓷】专家,【结构陶瓷】厂家直销,价格有优势;【结构陶瓷】成型/烧结/精密加工工艺成熟、交期准、保障质量,欢迎来电咨询:13412443344/0769-33235150/QQ2712136085科众工业陶瓷厂是【结构陶瓷】专家,【结构陶瓷】厂家直销,价格有优势;【结构陶瓷】成型/烧结/精密加工工艺成熟、交期准、保障质量,欢迎来电咨询:13412443344/0769-33235150/QQ2712136085
地址:http://www.taocibang.cn/jishu/1189.html
本文“工程陶瓷新磨削工艺介绍(图)”由科众陶瓷编辑整理,修订时间:2020-05-25 17:13:21
科众陶瓷是专业的工业陶瓷加工生产厂家,可来图来样按需定制,陶瓷加工保证质量、交期准时!
- 上一页:工程陶瓷高速磨削技术
- 下一页:陶瓷厂加工新切深缓进给磨削工艺